RABBIT KNIFE CONVERSIONBack in March
2017, I converted a 4 inch length stiff blade
"Rabbit Knife" made by
Victorinox, whereby removing the Fibrox handle material and custom fit a
deer antler. I didn't take any pictures of the conversion and decided
to do another one with a photo pictorial essay.

I used the knife below last
hunting season and this 2018
hunting season
and it performed flawless for a blade thickness of only .063 inches.
The knife is reminiscence of the 1850s trapper and hunters patch knives used
to trim the excess material from the ole patch and ball in the black powder
era. Those knives were typically worn in a scabbard hanging from their
neck resting on the chest for quick access. A tight fitting
scabbard was necessary since there was no finger guard in place which a
scabbard strap would normally be used to secure the knife.

I had Harry
Savage of Saxis, VA make a custom sheath for this knife.
The blade fits into the custom made sheath
"tighter than two coats of paint." I also ground a
small recess in the handle aka finger guard for the safety strap to rest in
since there is no finger guard on this knife.
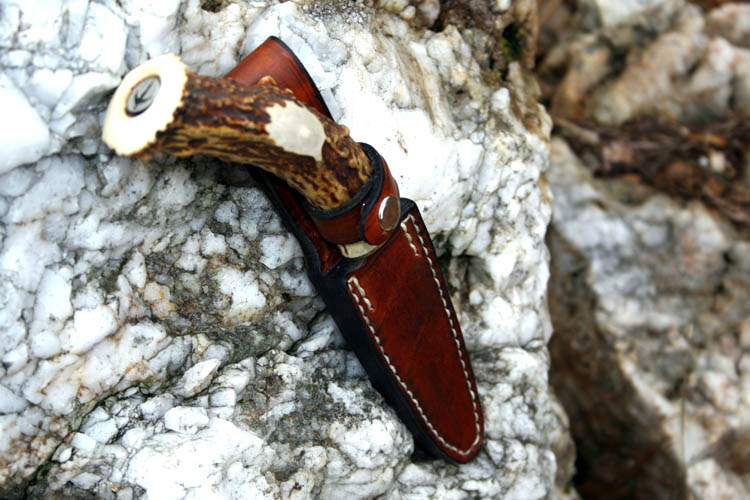
The knife handle will come from the lower set of antlers harvested on
12-10-18.

The antlers do not have the perfect crown at the base, but will make do
with what I have to work with.
PERSONAL SAFETY AND LIABILITY ISSUES
My goal will be to keep Safety
paramount because hand and power tools can do serious bodily harm and death
if not used properly, therefore these pages are solely for
entertainment purposes only from
a personal liability standpoint. Please read the
Legal Stuff
page for additional information concerning liability issues
before going any further. Safety glasses and hearing protection is a must,
although I do forgo the hearing protection many times; my bad!
BAND SAWED ANTLER TO LENGTH
I used my band saw to cut the antler length to 6 inches. The
smaller end where the knife blade shank will go into is a little over 1 inch
in diameter and should work ok. I plan to add a 1/4 inch thickness
brass finger guard which will be silver soldered to the blade.
I band sawed the brow tine off and used the 4 x 48 inch belt sander to
blend the base of the antler and the brow tine area. The shape of the
antler with the brow tine area not fully sanded flush makes a unique fit in
the right hand.
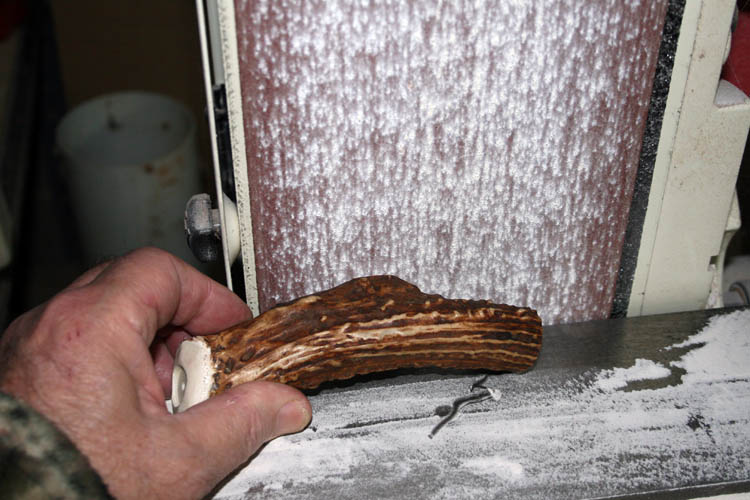
Below a few thumbnail pixs of the antler handle:
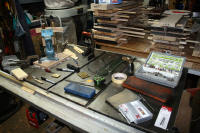
DRILLED HOLE FOR TURKEY TRACK MEDALLION
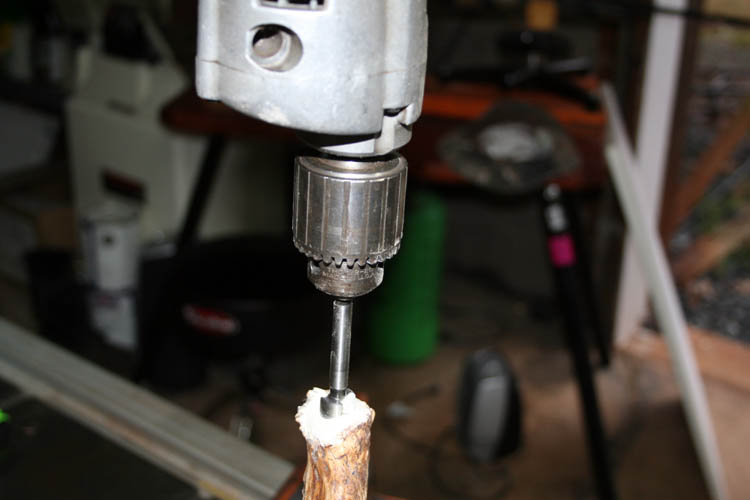
I used a .625 inch diameter Forstner drill bit for the turkey track
medallion. Something in the line of a deer medallion would be more
appropriate, but I have about 200 of those turkey track medallions on hand
for custom turkey box calls and will use what I have. It does add a
custom feature to the knife handle and you can use the knife to harvest the
breast from an ole Long Beard if desired too!
The above Milwaukee electric hand drill has been in service since the mid
1980s and still going strong, however the battery powered drills get far
more usage. I had to pull this drill out of retirement since both the
18V batteries for my DeWalt drills were dead and time to replace those
batteries due to not hold a charge for a month or two while setting idle.
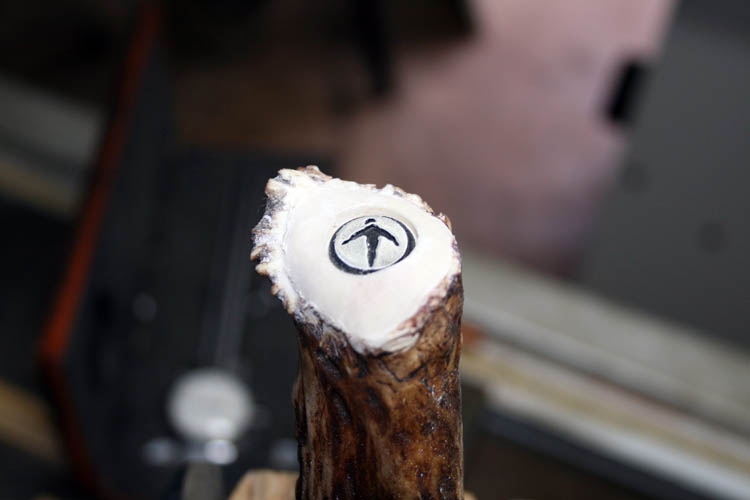
I will let the antler cure out a few weeks before I drill the final
diameter hole for the
knife tang. In the mean time, will remove the Fibrox handle from the
rabbit knife and regrind the shape of the knife tang. Any time you
grind on a knife blade that is already tempered, caution must be used not to
overheat the blade and destroy the blade temper aka hardness.
REMOVED FIBROX HANDLE
It is easy to get cut
removing the Fibrox knife handle which is molded in place, therefore will
tape the blade with a several layers of masking tape for protection.
The tang of the blade goes at least 2 inches into the Fibrox knife
handle.
Click on below thumbnail pixs for a larger screen view:
I drilled a series of holes in the Fibrox handle to ascertain its length
in the knife handle. I used a 1 x 24 inch belt sander to expose the
knife tang, I then used a chisel and hammer to separate the knife tang
from the Fibrox molded handle. The tang was ground rectangular and
rough ground it to around .070 +- inches. I dipped the blade into cold
water to keep from destroying the knife hardness. The manufacturer
ground the blade about 1/2 inch into the molded hidden tang and had to
square the shoulders of the blade off to the tang, otherwise the tang would
be too short for usage in the antler handle. The tang length now is 1
7/8 inches in length, of which the knife guard will use up 1/4 inch of that
which should leave enough tang to become firmly embedded into the antler
handle.
BRASS KNIFE FINGER GUARD SLOTTED
I used a piece of
1/4 x 2 x 4 inch length piece of brass to fabricate the knife guard.
The knife tang thickness is around .070 inches +- where the knife guard will
abut.
I used a carbide tipped scribe and rule to layout the knife tang hole/slot in the brass and
center punched a few witness marks for the drill bit. I then drilled
connecting 5/64 inch diameter drill holes and my scroll saw with a # 6
jewelers saw blade to connect the drill holes creating the slot for the
knife tang. I used a flat musical
instrument file to square the ends and fit the knife tang to the slot cut.
I rough sanded the brass knife finger guard using 400 grit wet/dry sand
paper.
Click on below thumbnail pixs for a larger screen view.
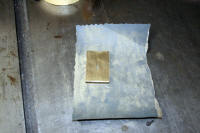
Next week, the Lord willing of course, I will pre-shape the finger guard profile and silver solder the knife tang to the brass finger guard
using Stay Brite low temperature solder and a propane torch. I don't think I need mapp
gas for this project.
Since the tang is a little over 1/16 inch in thickness, I plan to drill
several 1/8 inch diameter holes about 2 inches deep using a brad point drill bit in a vertical
orientation and have the antler handle anchored securely in my drill press
vise. There will be at least 1/32 inch clearance all around the tang
and route some angular holes into the handle for either epoxy or JB Weld to
grip. I will drill a small diameter hole into the bottom of the handle
into the cavity of to allow air to escape, otherwise
hydraulic action will try and push the knife tang back out of the filled
cavity with epoxy and/or JB Weld.
Web page
uploaded by Bill aka Mickey Porter on 12-21-18 and updated 12-22-18.
DRILLED HOLE FOR THE KNIFE TANG
I planned to
drill three 1/8 inch diameter holes into the knife handle, but elected to
drill a 3/8 inch diameter hole using a Forstner drill bit and grind a couple
slots in the handle for the excess knife tang width. The hole was drilled about 1.75
inches in depth. I used a tool and die makers small rectangular file
and the Dremel tool with a carbide cutter 1/8 inch in diameter to finish
fitting the knife tang to the handle. I routed several angular holes
into the inside cavity of the hole drilled to allow the epoxy a better
gripping surface, whereas the blade should never pull out of the cavity.
After checking the fit for
the knife tang to the handle, I traced around the antler onto the brass
finger guard and rough sanded the profile using a 6 x 48 inch belt sander and
1 x 42 inch belt sander. I used the PortaBand saw to cut the longer
end off the brass finger guard.
Below pixs of the hole layout
and drilling:
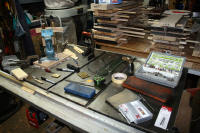
KNIFE GUARD TO BLADE
I started heating the
knife brass finger guard with the propane torch and after a little while,
solder was barely starting to flow, however the knife blade was discoloring too much and
stopped the process. There probably is a solder with a lower melting
point than the Stay Brite and might do some research if I decide to do
another knife handle conversion. The blade tang is only .070+- inches
thick and heated up quickly even with the flame directed toward the brass
finger guard. I will epoxy the guard in place with
the tang.
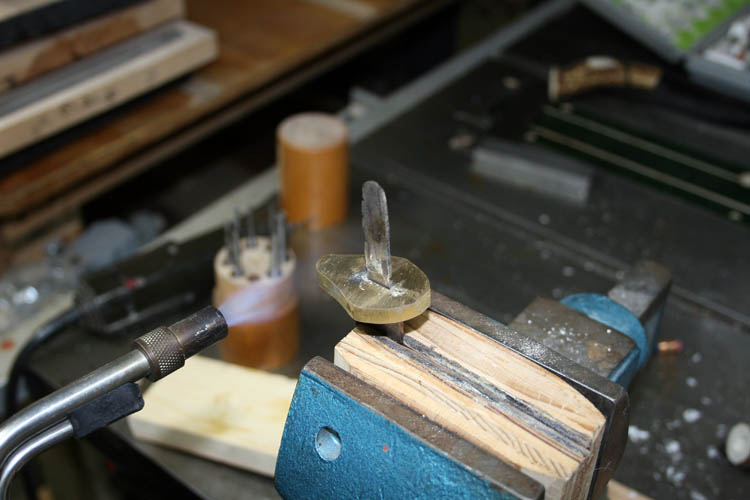
BLADE AND GUARD GLUED TO THE HANDLE
I mixed up some Epoxy 330 and glued the knife
blade, finger guard and tang to the antler handle.
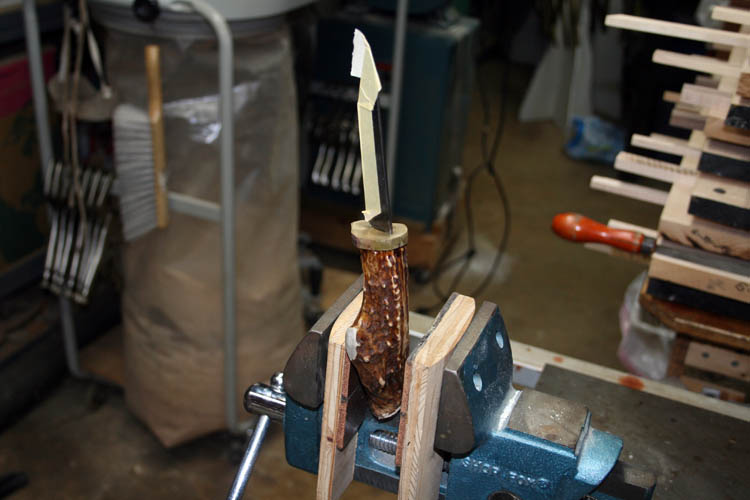
I will let the epoxy cure out over
night and start the final shaping and polishing of the finger guard.
GLUED
TURKEY TRACK MEDALLION
I glued the turkey track medallion in the handle.
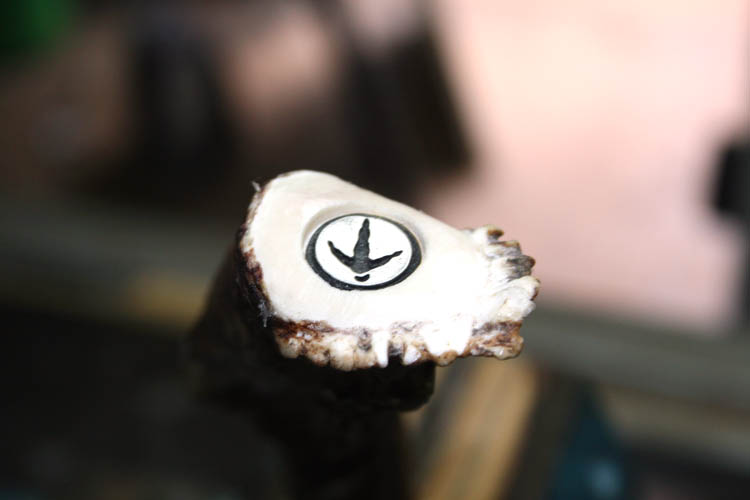
Below pix of the knife curing out:
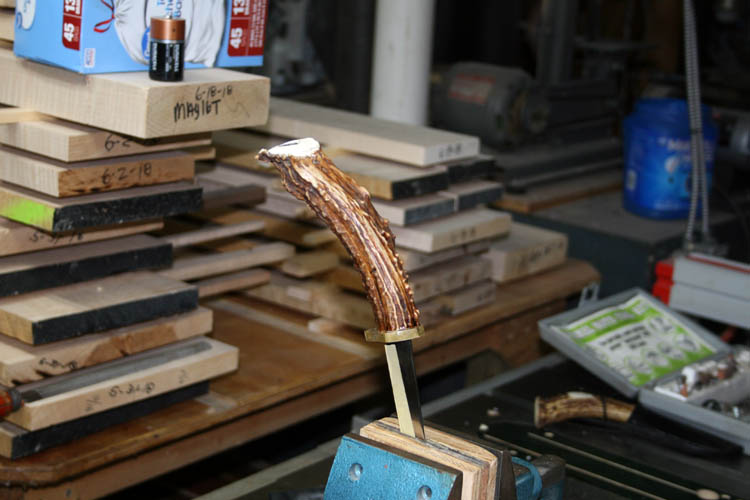
Tomorrow, the Lord willing of course,
I will start the final shaping/sanding of the brass finger guard.
Web
page updated by Bill aka Mickey Porter on 12-31-18.
FINAL SHAPING AND SANDING
I used my 6 x 48 inch belt sander and
the smaller 1 x 42 inch belt sander to final shape the finger guard along
with a fine file and 400 grit wet/dry sandpaper. I didn't want to
bring out the large
buffer/wheels which is stored and mainly used for musical
instruments and small wood projects. I might later sand the brass
finger guard with 600 or 800 wet/dry paper.
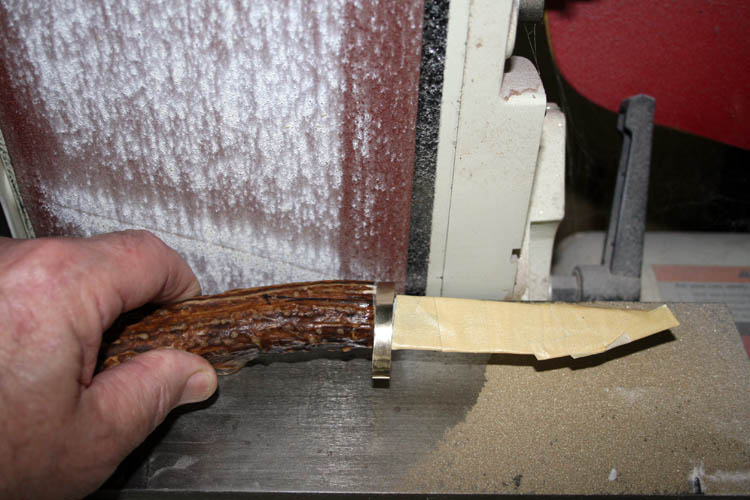
I taped the blade for safety and hopeful keep the blade off the sanding
belt.
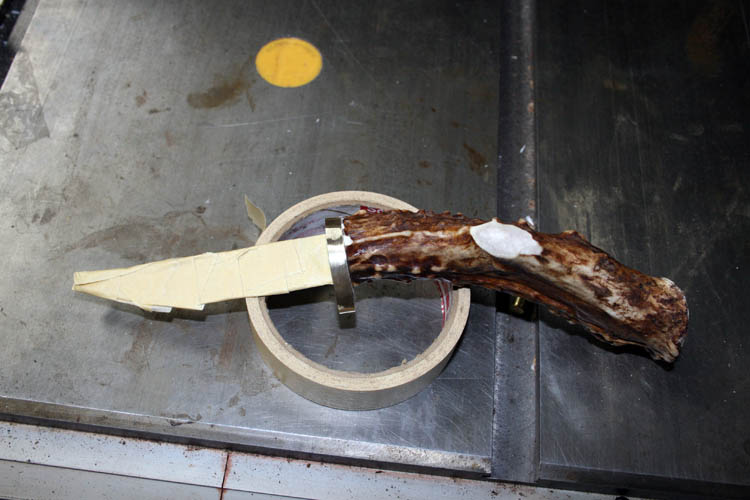
FINISHED KNIFE
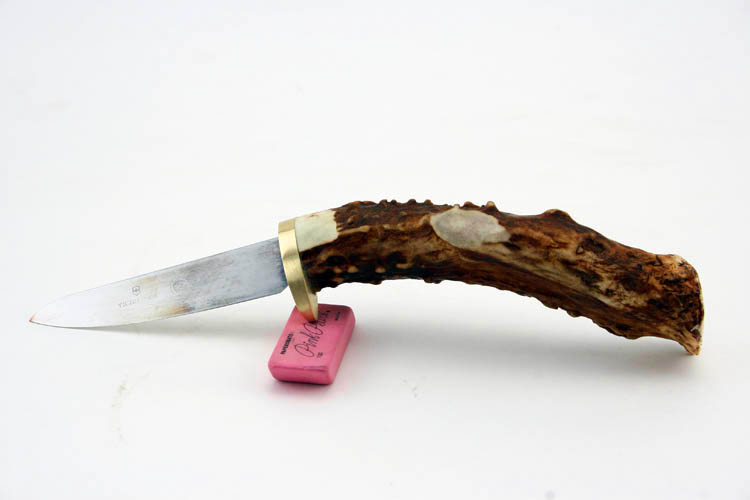
The antler handle fits my hand very well. The antler is very wide and
somewhat flat in the middle and the word of the day is
ergonomics. The final knife blade length is 3 7/8
inches with a width of 7/8 inch and blade thickness .063 inches.
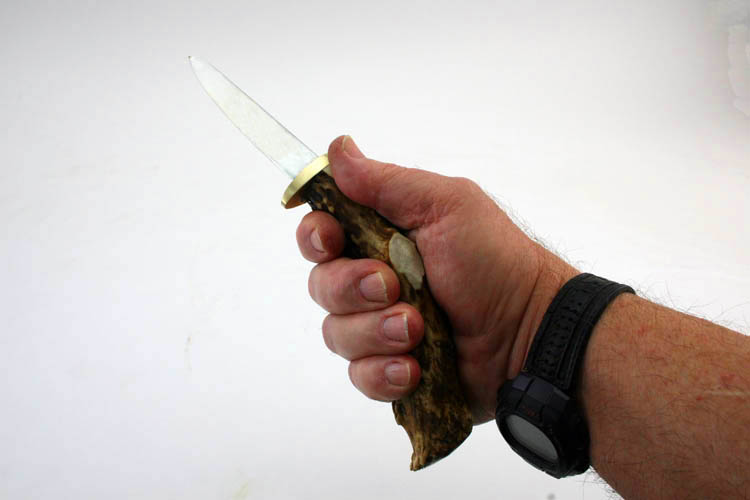
I hope to get a chance to field dress a few deer with this knife during the
2019 big game hunting season, our Lord willing of course!
Tomorrow is promised to no one.
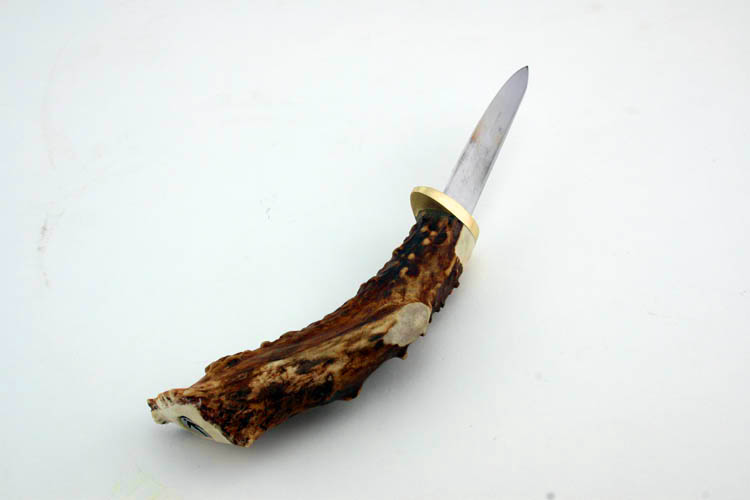
I definitely enjoyed converting the Victorinox Rabbit knife and will see
what kind of scabbard I can get for the knife.
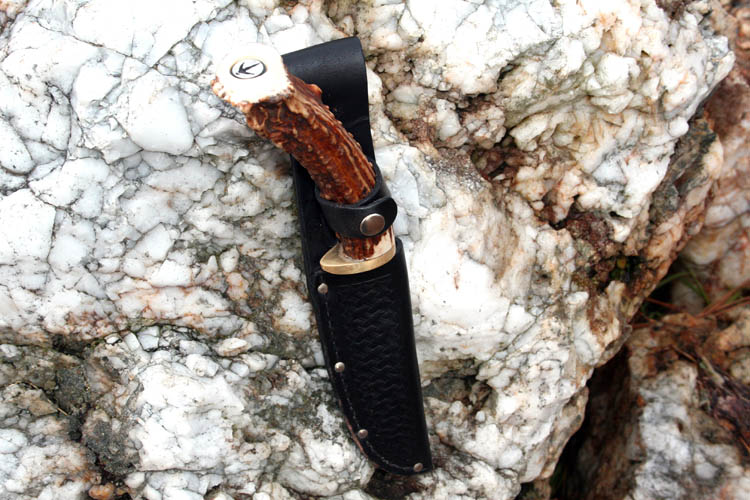
I located a scabbard aka sheath that I used to hold a modified Chicago
Cutlery knife and relocated the snap tie down strap.
Web page updated by Bill aka Mickey Porter on 01-01-19.
KNIFE HANDLE MODIFICATION
NOTE: I shortened the handle of the above knife 1.125 inches and reduced the
side to side thickness since the knife protruded to much outward by the
shape of the handle from the sheath aka scabbard. I also ground three
small finger grooves into the handle.
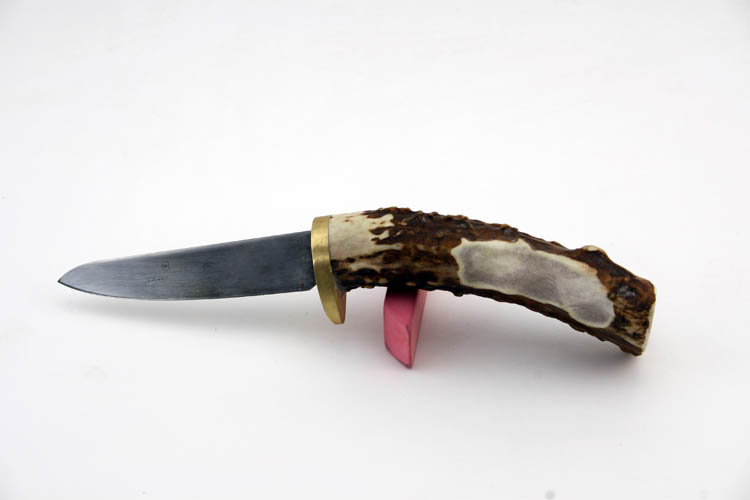
I plan to contact
Harry Savage of Saxis, VA and have him make
a custom sheath for this knife.
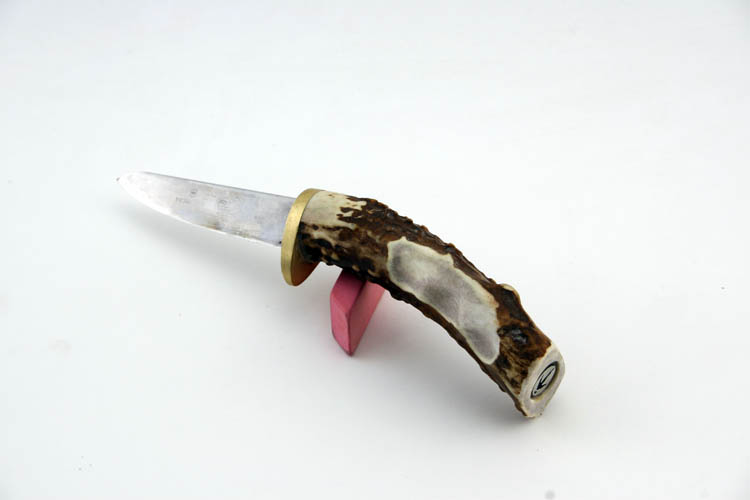
I like the handle shape and size much better.
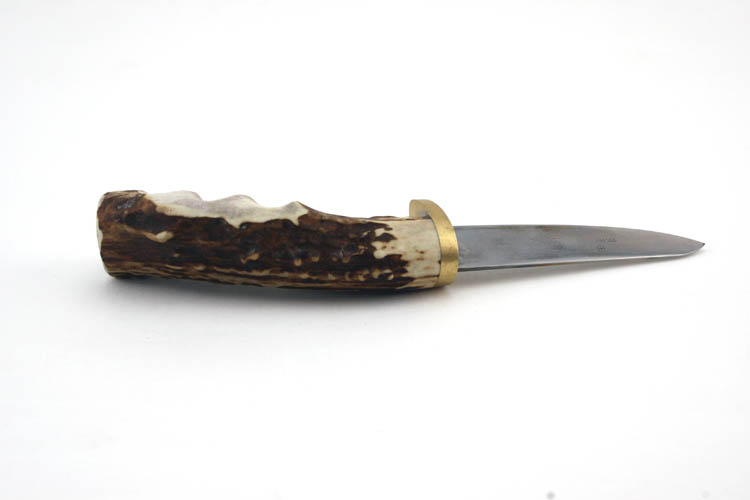
I got a chance to use the knife on 01-19-19 skinning/dressing eleven (11)
rabbits.
The drop/spear point is really an asset when inserting the tip into the body
cavity and moving the knife forward without cutting into the intestines or
stomach.
Web page updated by Bill aka Mickey Porter on 01-26-19.
HARRY SAVAGE CUSTOM SHEATH
I had Harry Savage of Saxis, VA make a custom sheath for the above knife.
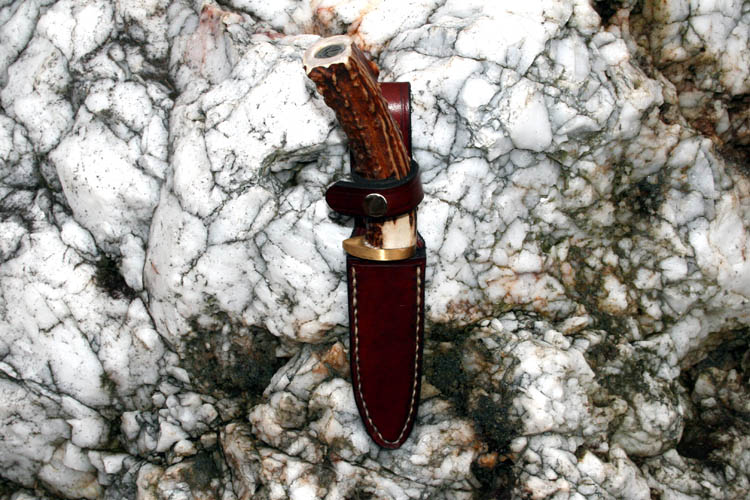
Mr. C. aka Calvin Jones with a good grin going!
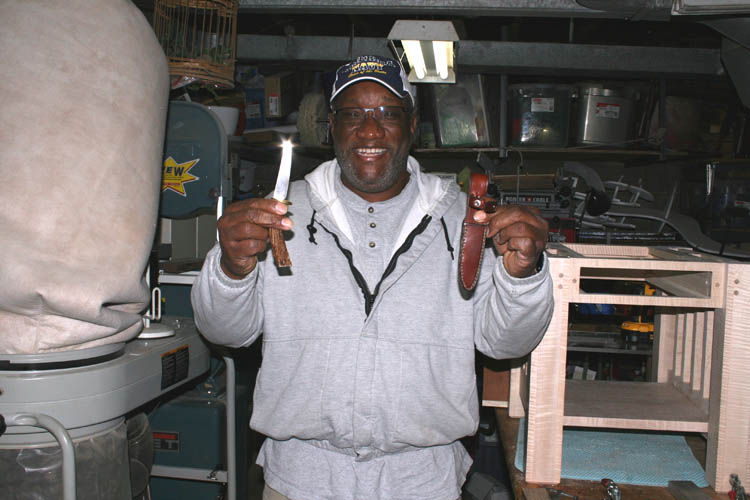
The above knife was gifted to one of my friends Calvin Jones on 03-09-19,
retired US Navy Senior Chief Petty Officer.
Web page updated by Bill aka Mickey Porter on 03-09-19.
CALVIN JONES KNIFE PIXS
Mr. C. aka Calvin Jones sent me several pixs of the knife gifted him and I
was impressed with them, therefore adding them to this page. I also
gave him the section that I removed from the deer antler knife handle to
shorten the length, of which will make a small paper weight or something.
I inlaid another turkey track medallion in the butt section of the deer
antler handle.
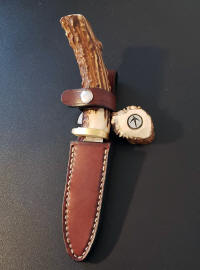
Web page updated by Bill aka Mickey Porter on 03-12-19.
ANOTHER KNIFE
I had one section of antler left from the 8 point buck harvest of 12-10-2018
and decided to make another field dressing and utility knife using a
Victorinox Kitchen Knife 6 inch stainless steel wide stiff blade.
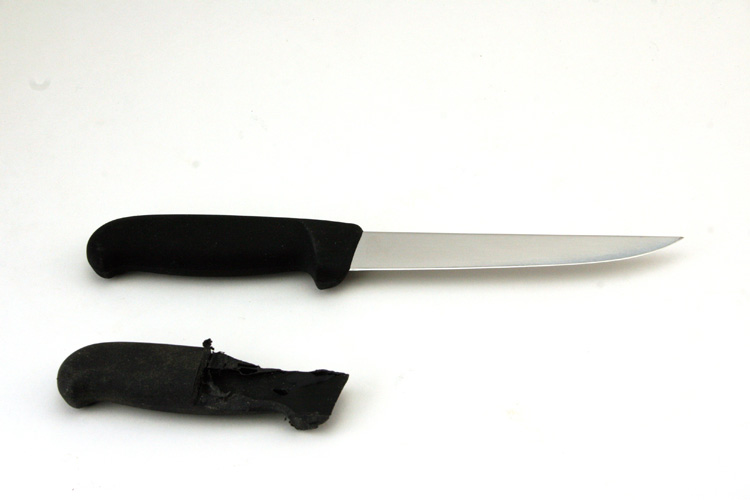
I did not take sequence pixs of the modification of the Victorinox knife
which basically the procedures were identical to the knife I made for Calvin
Jones annotated above.
I shortened the blade to 5 3/16 inch length for usage as a utility knife as
well. For field dressing deer, a blade length around 4 to 4.5 inches
is the ideal length in my humble opinion.
My 35MM DSLR camera body mirror definitely needs another cleaning
since there are dust spots showing in the above pix, especially on the upper
left hand portion of the pix. I will address that issue in the very
near future!
During the fabrication of the handle, I had some difficulty getting the
blade tang which had to be reground to about 3/8 inch in width to properly
align with the 3/8 inch hole I drilled in the antler. The hole was not
drilled "perfectly" for proper blade orientation, but made it work with some
"wallowing" out the antler drill cavity. I had to change the grind
angle on the handle that abutted the knife brass finger guard and it
shortened the length of the knife handle more than I like for my large hand,
but it will still work....not the best job I have done, but I didn't want to
discard the antler handle...........grin if you must!
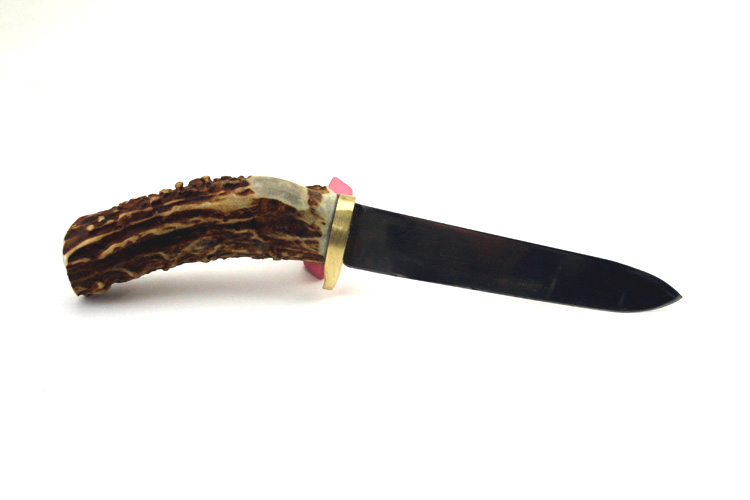
The tip of the knife resembles more of a spear point and/or drop point which
will work great for field dressing a deer, whereas the tip of the blade is
below the spine of the blade.
I am having Harry
Savage of Saxis, VA make a custom sheath for this knife and will
post a pix when the sheath arrives.
Web page updated by Bill aka Mickey Porter on 02-26-2021.
DIDN'T LIKE THE ANTLER HANDLE
I wasn't pleased with the above antler handle since it was too short for my
large hand. I had a shed antler that is at least 40 plus years old
that was found behind our
home on White Store Road and decided to use it.
It was just large enough to fit the finger guard on the above knife.
I band sawed slots into the handle the length of the recessed knife tang and
worked it loose with a chisel. The epoxy glue did a good job holding
the tang into the handle. I gave the handle portion left to our
Grandson Xander McKnight Gonzales, of which had a turkey track medallion
inlaid into it and also the rest of the shed antler that wasn't used.
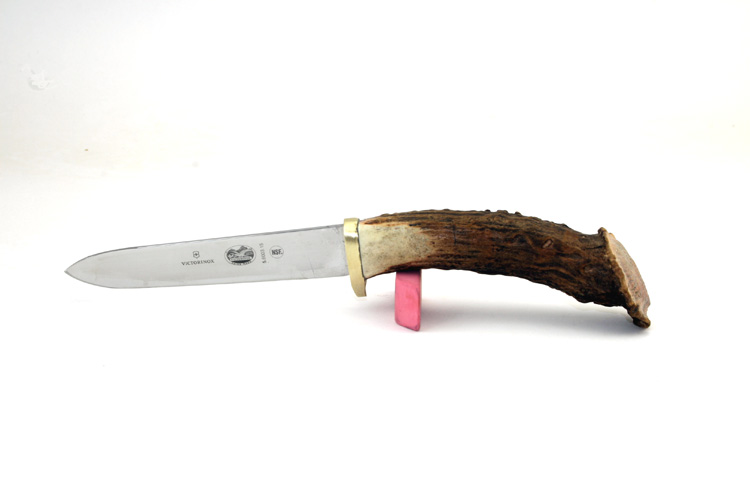
This antler crown handle fits my hand very well and has much more overall
eye appeal in my humble opinion. I will give this knife a field test this coming hunting
season, our Lord willing of course.
Web page updated by Bill aka Mickey Porter on 03-03-2021.
KNIFE WITH HARRY SAVAGE CUSTOM SHEATH
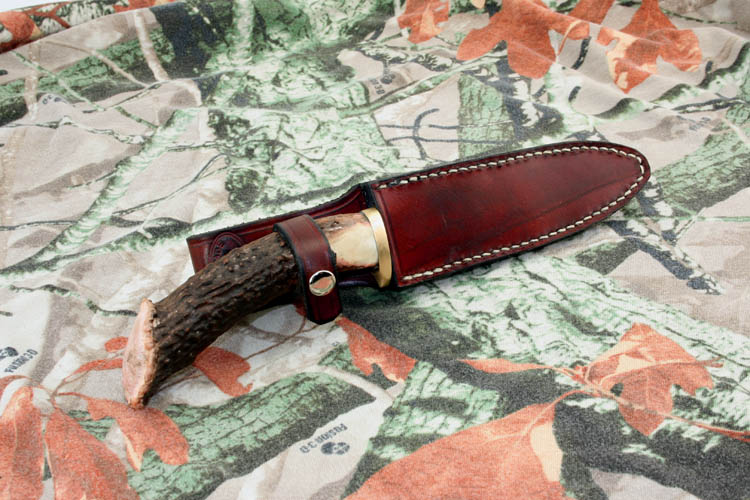
INLAID INDIAN HEAD NICKEL
I inlaid a Indian Head Nickel in the antler crown handle. I couldn't
find the correct size bit to drill the cavity, but purchased a 7/8 inch
diameter Forstner drill bit that would work, however oversized.
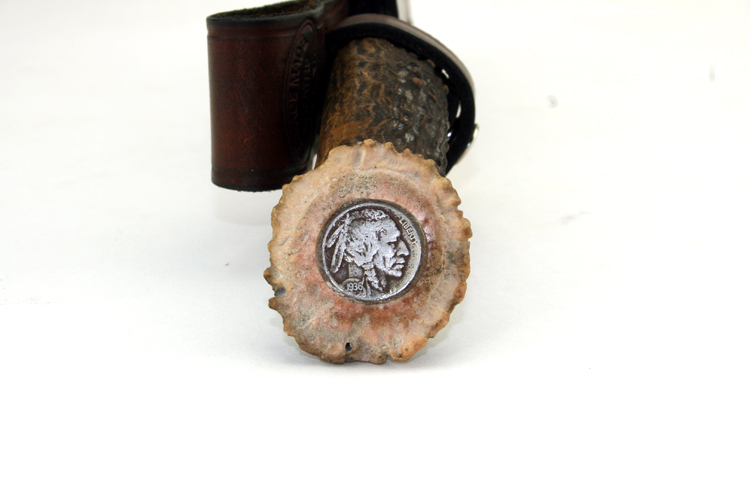
I had about forty (40) Indian Head Nickels and only half a dozen wasn't worn
too badly. The mint date on the Indian Head Nickel is 1936.
Our government certainly did the Native American Indians wrong and practiced
genocide via
manifest destiny and wiped out entire
cultures of them, yet "we" point the fingers at other countries for
committing the same type of
inhumane crimes!
I would not trust a Bureaucrat aka Stupacrat regardless of party affiliation and
their die hard supporters in an outhouse with a muzzle on.
Native Americans summed Washington and it's Bureaucrats up very well
during the period of their
systematic destruction during the second half of
the nineteenth century, "White man speak with forked tongue."
For a Native American History Lesson with controversial evidence and
documentation, read
Bury My Heart At Wounded Knee by Dee Brown which might open your
political blindness. It is estimated that between 80 to 100 million
native Americans have died since European settlers came to North and South
America by various diseases and outright genocide.
Looking forward to using this knife in the future, our Lord willing of
course.
Web page updated by Bill aka Mickey Porter on 03-05-2021 and 03-08-2021.
LEAVING ON A
SPIRITUAL NOTE
If you do not know Jesus Christ as your Lord and Savior, please take
this moment to accept him by Faith into your Life, whereby Salvation
will be attained.
Ephesians 2:8 - 2:9 8 For by grace are ye saved through
faith; and that not of yourselves: [it is] the gift of God: 9 Not of
works, lest any man should boast.
Hebrews 11:1 “Now faith is the substance of things hoped for,
the evidence of things not seen.”
Romans 10:17 “So then faith cometh by hearing, and hearing by
the word of God.”
Open this
link about faith in the King James
Bible.
Romans 10:9 “That if thou shalt confess with thy mouth the
Lord Jesus, and shalt believe in thine heart that God hath raised him
from the dead, thou shalt be saved.”
Open this
link of Bible Verses About Salvation,
King James Version Bible (KJV).
Hebrews 4:12 “For the word of God is quick, and powerful, and
sharper than any two edged sword, piercing even to the dividing asunder
of soul and spirit, and of the joints and marrow, and is a discerner of
the thoughts and intents of the heart.”
Romans 6:23 “For the wages of sin is death; but the gift of
God is eternal life through Jesus Christ our Lord.”
Romans 3:23 “For all have sinned, and come short of the glory
of God;”
Micah 6:8 “He hath shewed thee, O man, what is good; and what
doth the LORD require of thee, but to do justly, and to love mercy, and
to walk humbly with thy God?”
Philippians 4:13 "I can do all things through Christ which
strengtheneth me."
